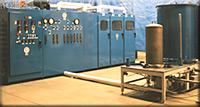
Tool Coating System
|
Carbide and tool steels can be enhanced for wear resistance
by Chemical Vapor Deposition (CVD) of thin-film, diffusion bonded
coatings. These coatings result from the reaction between various
gaseous phases and the heated surface of a substrate. The coating
is hard, wear-resistant and bonded to the substrate.
COATING PROCESSES
Typical compositions of CVD coatings are:
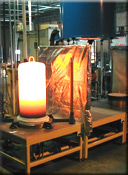
Tool Coating Retort |
The titanium coatings are formed by reacting
titanium tetrachloride (TiCl4) with mixtures of nitrogen
(N2) or carbon (C) containing gasses such as N2
and methane (CH4), in varying portions to tailor the
composition of the coating to the application.
H2 + TiCl4 + CH4 = TiC + 4HCl + H2
2H2 + 2TiCl4 +N2 = 2TiN +
4HCl
H2 + 2TiCl4 + N2 + 2CH4
= 2TiCN + 8HCl + H2
|
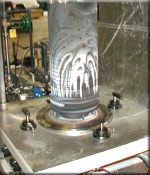
Tool Coating Fixtures |
Aluminum oxide (Al2O3) is a two-step process formed
by the reaction of aluminum trichloride (AlCl3) with carbon dioxide
(CO2) to form the Al2O3. The AlCl3 is formed in an external halide
gas generator by passing hydrogen chloride (HCl) gas over pellets
containing aluminum.
2Al + 6HCl + H2 = 2AlCl3 + 4H2
4AlCl3 + 3CO2 + 13H2 = 2Al2O3
+12HCl + 3CH4 + H2
Applying multiple layers of different combinations
of these compounds creates specialized coatings.
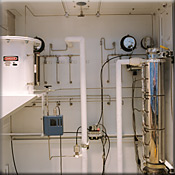
Halide Gas Generator |
TOOL COATING FURNACE SYSTEM
A typical coating furnace system is comprised
of an electrically heated furnace; a reaction chamber (retort);
specialized fixtures for the parts to be coated; vacuum system (for
aluminum oxide process); gas delivery system; halide gas generator
(for aluminum oxide process); fume neutralization system (scrubber)
-- all controlled by a microprocessor based automated or semi-automated
control system.
The furnace systems can be either bell type
(a moveable furnace that gets lowered over the fixtured parts),
or a top loading system (fixtured parts get lowered into a stationary
furnace).
|