Fluoride Ion Cleaning (FIC), synonymous with Hydrogen Fluoride
(HF) Ion Cleaning, has been proven to be a highly effective process
for the removal of deeply embedded oxides from superalloys containing
significant amounts of aluminum and titanium.
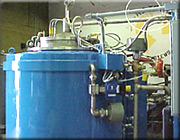
Top Loading FIC System |
APPLICATIONS
Gas turbines require regular overhaul to ensure optimum
performance and efficiency. Hot section engine components are subject
to damage and deterioration from one or more of the following:
Repairs require the addition of new material applied
by welding and/or brazing. The FIC process is the best cleaning
process for the removal of deeply imbedded oxides prior to weld
or braze repair.
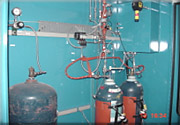
HF Delivery System |
THE FIC PROCESS
The process results from the reaction of fluorine
with various oxides that are formed on the parts. At temperatures
greater than 1750° F (950° C), the fluorine reacts with
oxides that have formed on the surface of the turbine components,
converts them to fluorides, and allows for their removal. This leaves
behind a clean surface as a preparation step for vacuum brazing
and other repair processes. The chemical reactions are illustrated
by the following:
6 HF + Al2O3 = 2 AlF3
+ 3 H2O
4 HF + TiO2 = TiF4 +
2 H2O
6 HF + Cr2O3 = 3 H2O
+ 2 CrF2 + F2
In addition to the removal of oxides from the
surface and within cracks, surface depletion of elements such as
titanium and aluminum also occurs which enhances brazeability by
removing oxide reformers. These reactions are illustrated by the
following:
6 HF + 2Al = 2AlF3 + 3H2
8 HF + 2Ti = 2TiF4 + 4H2
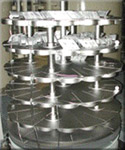
FIC Fixtures |
FEATURES
The significant feature of our systems is the generation of the
fluorine containing atmosphere independent from the component temperature
inside the reactor (retort). This process is referred to as Dynamic
Fluoride Ion Cleaning (DFIC). The reaction temperature, concentration
of fluorine, pressure level, and duration are all independently
controlled variables. This state of the art process has been proven
to be more effective and repeatable than older processes based on
the decomposition of fluorine containing compounds.
A unique feature of our systems is the ability to perform the FIC
process at sub atmospheric pressure from 100 to 650 Torr (133 to
867 Millibar) while at processing temperature. This process is referred
to as dual vacuum. The dual vacuum process has been proven to be
the most effective method of cleaning heavily oxidized parts. This
is accomplished by creating a vacuum on both the retort and the
furnace (required to prevent collapse of the retort while at temperature
from the forces of the vacuum). The dual vacuum process has been
found to be extremely effective in cleaning cooling channels, small
cracks and blind holes. By changing the pressure level in the retort,
HF gas is forced into cooling channels, small cracks and blind holes.
Another benefit of the dual vacuum process is that it utilizes significantly
less HF than the atmospheric FIC process.
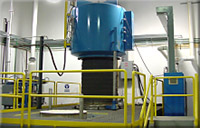
Bell Type FIC System |
FIC FURNACE SYSTEM
A typical FIC system is comprised of an electrically
heated furnace; a reaction chamber (retort); vacuum system; hydrogen
and argon delivery system; gaseous HF delivery system; fume neutralization
system (scrubber) -- all controlled by a microprocessor based automated
control system.
The furnace systems can be either bell type
(a moveable furnace that gets lowered over the fixtured parts) or
a top loading system (fixtured parts get lowered into a stationary
furnace).
|